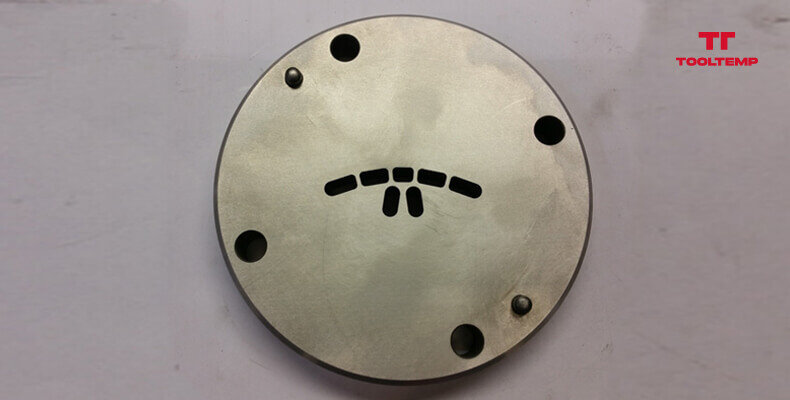
Alles wat je moet weten over het extrusieproces
Extruderen is een vormgevingstechniek waarbij een vervormbaar materiaal door een matrijs geperst wordt. Deze techniek wordt extrusie of extrusietechnologie genoemd.
Wat is extrusie
Kunststofextrusie is een continu of discontinu proces waarbij de kunststof in een schroef plastisch wordt gemaakt en wordt gemengd met de benodigde additieven om bepaalde materiaaleigenschappen te verkrijgen. Het proces is continu bij het maken van bijvoorbeeld buizen en discontinu bij het maken van bijvoorbeeld pet flessen. Onder hoge druk wordt de kunststof door een matrijs geperst waardoor een product ontstaat zoals bijvoorbeeld een buis, een profiel, een kabel, etc.
De extrusie van kunststofproducten in 6 stappen
Het (indien nodig) drogen van het kunststofgranulaat om het vervolgens te transporteren naar de extruder (soms is het nodig om additieven bij te mengen zoals bijv. kleurstof).
- Het invoeren van het granulaat in de schroef van de extruder;
- Het mengen en transporteren van de kunststof in de schroef naar de neus van de schroef;
- Het plastisch maken van het granulaat in de schroef door verwarming en frictie;
- Het persen van de kunststof door een matrijs;
- Het uitharden (afkoelen) van de kunststof als deze uit de matrijs komt, door afkoelen aan de omgevingslucht of door geforceerd koelen met koelwater;
- Het op de gewenste lengte brengen van de kunststofproducten.
De extruder
De extruder bestaat uit de volgende delen:
Plastificering
Dit betreft de schroef en de cilinder waarin de schroef zich bevindt.
De schroef zorgt voor het smelten van het kunststofgranulaat en het mengen van de additieven in deze smelt. Dit gebeurt door elektrische verwarming van de cilinder en frictie in de schroef. Door de druk opgebouwd in de schroef of door een constante druk opgebouwd in een meltpomp wordt de kunststof door een matrijs geperst.
Matrijs
In dit deel van de machine wordt de kunststof (continu) gevormd naar het gewenste product. Afhankelijk van de verschillende producten zijn er diverse extrusietechnieken. Het product wordt afgekoeld nadat het uit de matrijs is gekomen.
Het extrusieproces
De belangrijkste delen van het extrusieproces zijn:
- Het plastificeren en mengen van de kunststof.
- Het onder de juiste omstandigheden (temperatuur en druk) persen van de kunststof door de matrijs.
- Het uitharden van de kunststof.
Al deze processen moeten zo efficient mogelijk worden gedaan om de capaciteit (output) van de extruder zo hoog mogelijk te houden. Uiteraard mag dit geen afbreuk doen aan de kwaliteit van het (eind-)product.
De extrusiematrijs
De extrusiematrijs is belangrijk in het extrusieproces. De “kwaliteit” van deze matrijs is in grote mate bepalend voor de kwaliteit van het eindproduct en de efficiëntie van de extruder.
- Links een voorbeeld van een extrusiematrijs die wordt gebruikt in een continu proces;
- Rechts een blaasextrusiematrijs, deze worden gebruikt in discontinue processen, bijvoorbeeld bij het maken van plastic pet flessen.
Belang van temperatuurbeheersing
Bij het extrusieproces moeten de cilinder en de schroef op een zekere (materiaalafhankelijke) temperatuur worden gebracht om het extrusieproces te kunnen starten. De temperatuur van de cilinder verschilt per zone omdat in de schroef verschillende processen plaatsvinden:
- Het invoeren van het kunststofgranulaat.
- Het plastificeren van het kunststofgranulaat.
- Met mengen van de verschillende additieven met de kunststof.
- Het (bij sommige kunststoffen) ontgassen van de melt.
- Het comprimeren van de kunststof.
Gedurende het proces is het van belang dat de cilinder op de juiste temperaturen wordt gehouden zodat de kunststof zo optimaal mogelijk wordt verwerkt. Het is ook van belang dat het proces zo constant mogelijk verloopt en een constante druk opbouwt zodat het eindproduct constant is van kwaliteit en een zo hoog mogelijke output wordt gehaald.
Bij verschillende extrusietechnieken is het van belang om ook de temperatuur van het product te controleren als deze uit de matrijs komt en “verwerkt” wordt tot eindproduct.
- Bij het extruderen van profielen moeten deze vaak gekoeld worden (in waterbakken) om deze op de juiste temperatuur te brengen zodat ze kunnen worden ingekort en verpakt;
- Bij het extruderen van folie en plaatmaterialen wordt de kunststof als deze uit de matrijs komt over walsrollen gevoerd om de kunststof op temperatuur te houden of juist gecontroleerd af te koelen.
Wat kan er fout gaan
- De kunststof wordt bij het invoeren in de schroef te warm waardoor deze plastificeert en niet meer of niet snel genoeg in de schroef gevoerd kan worden. Koeling van de intrekzone is vaak noodzakelijk om een snelle invoer te kunnen waarborgen;
- De temperatuur in de cilinder is te laag waardoor de kunststof niet goed plastificeert of niet goed mengt met de additieven waardoor het product niet voldoet;
- De kunststof wordt in de cilinder te warm waardoor deze kan verbranden en bepaalde eigenschappen kunnen veranderen. Het is dus van belang dat de cilinder op de juiste verwerkingstemperaturen wordt gebracht en gehouden om de kwaliteit te kunnen garanderen en de output zo hoog mogelijk te houden;
- De walsrollen blijven niet constant op temperatuur of de temperatuur over de lengte van de walsrol varieert te veel. Het tempereerapparaat levert niet voldoende verwarm- en/of koelcapcaciteit of de pompcapaciteit is te laag waardoor het water of de olie niet snel genoeg door de walsrol stroomt en daarmee de temperatuur niet voldoende constant kan houden.
Het extrusieproces verbeteren
Om het proces te verbeteren dien je de juiste methode van verwarmen en koelen te kiezen.
- Het koelen van de intrekzone wordt vaak gedaan met water uit het centrale koelsysteem waardoor de temperatuur niet ingesteld kan worden maar afhankelijk is van het beschikbare koelwater en waardoor in veel gevallen corrosie optreedt en het koelkanaal na verloop van tijd dichtslibt en de koelcapaciteit lager wordt;
- Het verwarmen van de cilinder wordt in de meeste gevallen gedaan met elektrische verwarmingselementen. In sommige gevallen wordt gekozen voor het verwarmen met water (onder druk) of olie (voor hogere temperaturen). Erg belangrijk is een exacte meting van de temperatuur per zone omdat deze waarde wordt gebruikt voor het verwarmen of koelen van de cilinder. Als deze meting niet klopt, is het proces niet goed te beheersen. Ook is het van belang om regelmatig te controleren of de verwarmingselementen nog goed functioneren. Deze kunnen door ouderdom of foutieve montage doorbranden;
- Bij sommige kunststoffen moet in het proces naast verwarmen (vooral bij de opstart van het proces) ook warmte worden afgevoerd die ontstaat door de wrijving van de kunststof in de schroef/cilinder. Hiervoor wordt koeling d.m.v. water of lucht toegepast waarbij water in de meeste gevallen een hogere koelcapaciteit kan brengen. Het nadeel van waterkoeling is het ontstaan van corrosie en verkalken van de leidingen waardoor de leidingen dichtslibben en de koelcapaciteit achteruit gaat;
- Door voor het verwarmen tempereerapparaten op thermische olie in te zetten, kan met extern koelwater ook de thermische olie en daarmee het proces gekoeld worden. Op deze manier kan een hoge koel- en verwarmingscapaciteit worden verkregen. Het nadeel van thermische olie is de hoge temperatuur van diverse slangen en de kans op lekkages als koppelingen niet goed worden aangesloten. Ook veroudert de olie op termijn en moet deze dan vervangen worden. het voordeel is dat er geen problemen kunnen optreden met corrosie en verkalking.
Extrusietechnieken
- Folie-extrusie
- Plaatextrusie
- Profielextrusie
- Blaasvormextrusie
- Compounderen